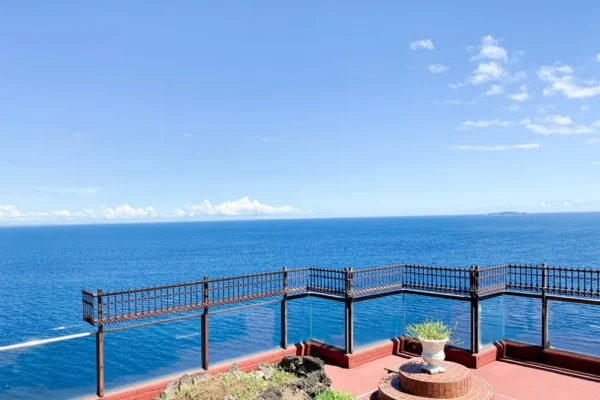
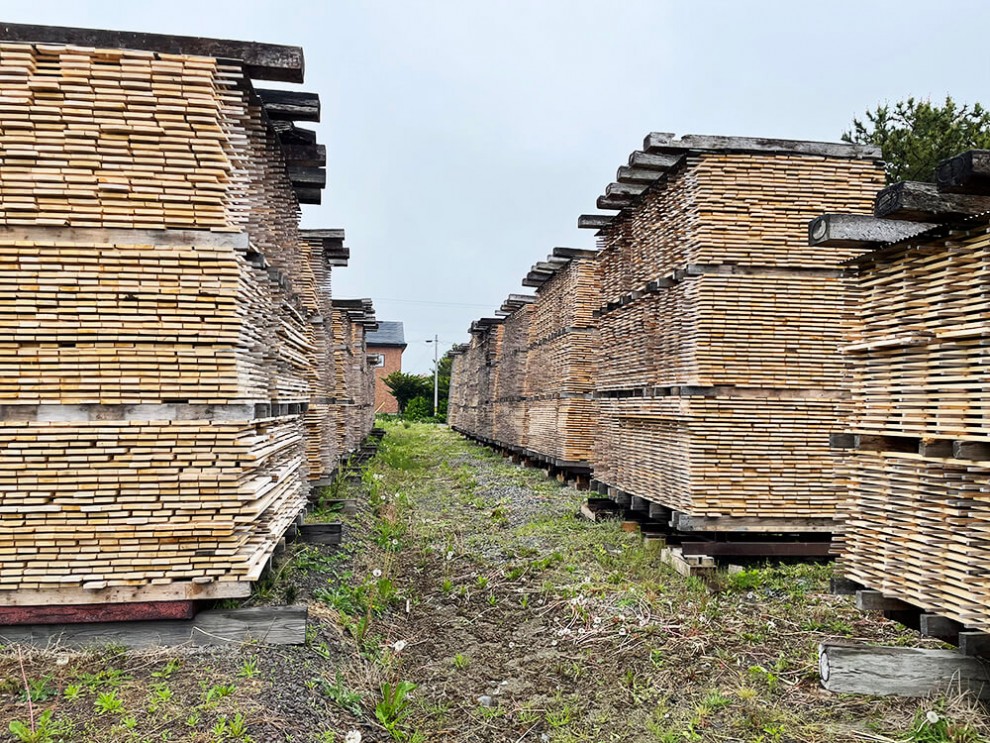
こんにちは。リノベーションプランナーの遠藤です。
暑い夏が過ぎ、今年も残るところわずか。年々、1年が過ぎる速さの体感が早まっている気がします。一日一日を大切に過ごしてゆきたいものです。
さて、今回の記事は前回レポートさせて頂いた1泊2日の北海道旅の後編です。
前回の記事では、1本の木ができるまでの過程としての「植林体験」について書かせて頂きました。今回の記事では、植えた木が成木となってから住まいづくりに欠かせない「フローリング」になるまでの過程について書かせて頂きます。
いつもリノベーションをさせて頂く際に使わせて頂いている「無垢フローリング」がどのようにつくられているのか、初めて実際に間近で見ることが出来ました。
1本の木がフローリングとなり、私たちのもとへ届くまでのヒストリーを知ることのできた貴重な経験でした。
目次
フローリングがつくられている場所。ウッドファミリー
工場の味わいある佇まいがかっこいい
北海道の知内(しりうち)にある「ウッドファミリー」というフローリング工場で、夢工房の家づくりでいつも使わせて頂いている「チャネルオリジナル」さんの無垢フローリングがつくられています。
北海道の各製材所からここウッドファミリーに広葉樹の原板が集まり、フローリングがつくられていきます。
工場裏には津軽海峡が広がる
工場の近くには森があり、すぐ後ろには津軽海峡が広がる豊かな環境の中でフローリングが製造されています。
研修2日目に訪れたこちらの工場で、広葉樹が原板からフローリングになり、梱包されるまでの過程を学ばせて頂きました。
森と海に囲まれた知内の町とそこでのフローリングづくりを目の当たりにして身をもって知れたことは、森と海は繋がっているということ。そしてその森と海があることによってものづくりができているということ。
豊かな森の養分が豊かな海をはぐくみ、豊かな海からの雨風がまた森を豊かにするという循環の中で、木々が育ち家づくりをすることができています。自然に感謝です。
フローリング制作の道のり:原板の受け入れ~乾燥
①津軽海峡の風で自然乾燥
工場に入荷され、うず高く積み上げられた原板たち。
原板からフローリングとして製品になるまでには多くの工程があり、期間としては約4~5か月かかります。
北海道の各製材所から受け入れられた原板たちは、乾燥させるために上の写真のように、一枚一枚揃えて積み上げられていきます。
木は水分を含んでいるので、乾燥させて水分を飛ばすことで木が固く強くなります。
乾燥にも2つの工程があり、まずは①自然乾燥され、次に②人工乾燥されます。
広葉樹はいきなり火にかけると割れてしまうので、2つの工程で丁寧に乾燥されてゆきます。
津軽海峡の海風で3か月~4か月、じっくりと乾燥。
自然乾燥のために1枚1枚積み上げられていく様子。
自然乾燥中の原板。均等に積み上がっている様子は見応えがある。
センの原板。
②乾燥窯で人工乾燥
人工乾燥庫の様子
自然乾燥が終わったら、窯と乾燥機で乾燥させてゆきます。
レンガ積みの乾燥窯。長く使い継がれている。
ウッドファミリーで使われている乾燥窯はレンガが積まれてつくられたもので、40年以上前のもの。レンガ積みの乾燥窯としては日本で一番古いものだと言われているそう。
レンガが崩れてしまった時には手で直して、長く使い続けられている、フローリングづくりに無くてはならない窯。
1つしかないこの窯で1枚1枚のフローリングがつくられていることを知ると、思い入れが強くなります。
この窯の燃料としては、木の根や木の皮などの廃材や使われないフローリング材が再利用されています。化石燃料は使われていません。
ウッドファミリーでは、出来る限りごみを出さずに、循環型のものづくりがされています。製造の各工程で出るおがくずやカンナくずなども廃棄せずに保管して、近くの酪農家さんたちが牛舎の敷き藁に使い、牛糞と混ぜて牧草畑の堆肥として撒いてくれているのだそう。
広葉樹のおがくずは腐りやすく土に還りやすい。そして無垢フローリングの廃材は接着剤や溶剤なども含まれていないので肥料に適しているんですね。
中低温乾燥機
乾燥機もまた味がありかっこいい。
乾燥機では70度の中低温(熱すぎると割れてしまうため)で乾燥させ、含水率の測定を行います。
フローリング制作の道のり:原板の加工~仕上げまで
③養生
材料がトロッコで移動されていく様子。
人工乾燥が終わったら、10日~2週間養生をします。
工場内には各所にレールがひかれており、材料はトロッコで移動されます。
養生された原板たち。
④フローリングの形になるまで
ここから加工がスタートしていきます。
フローリングの形になるまでに多くの加工の過程を踏みますが、どの工程も目でよく確かめられながら手作業で行われます。
加工工場の様子。
欠点の除去作業~節処理
欠点除去作業に使われる機械
最初に行われるのが「欠点除去」と呼ばれる作業で、割れや曲がり、反りなどの欠点を除去し長さが揃えられていきます。
「一次加工」ワイドサンダーの機械
次の「一次加工」で厚みが揃えられ、「二次加工」としてサイドマッチ加工が施され、必要な場合は節の処理も行われます。
◀サイドマッチ加工:フローリングを貼り合わせる際の実(さね)ができます
◀節のパテ処理のイメージ
仕上げの加工
「三次加工」二連式ワイドサンダーの機械
「三次加工」として、表面にサンダーをかけて仕上げます。この時に表面品質の確認を行い、表面の焦げやその他の欠点除去も行われます。
一次加工と三次加工の2回に分けてサンダーがけを行うというのが加工工程でのこだわりだそう。
そして、仕上げの最後「四次加工」としてエンドマッチ加工を行います。
エンドマッチ加工に使われる機械。加工工場の中で一番大きなマシーンです。
エンドマッチ加工はフローリングの短手両端の小口を綺麗にする作業。
目の前で加工の様子を実演して頂きました!
⑤梱包から出荷までも手作業で丁寧に
保管されているフローリング材と梱包の様子。
こうしてフローリング材として仕上げられた後、一枚一枚目視で表面検査がされています。
そして、仕上げの塗装も梱包もすべて手作業で行われています。
乱尺で長さの異なるフローリングが1800㎜の段ボールに納まるように組合されながら梱包されていく様子はまさに職人技。
塗装掛けがされている様子。
塗装も一枚一枚手作業です。こんなにも手間暇が掛けられているのかと、感動しました。
塗装は2回塗りで、1回塗って乾かした後にもう一度塗られます。
この塗装の作業は工場だけでなく、近くの障がい者施設にもお願いをしてご協力を頂いています。
こうしてようやく、1本の木が1枚のフローリングとなり、私たちの生活に届きます。
フローリングは自然に育まれ、手をかけられた宝物
私たちの家づくりに欠かせないフローリング。とても身近で当たり前のように使っているものですが、1本の苗を植え、長い歳月と手間暇をかけて出来上がる過程を体感し、目の当たりにして、材料へのリスペクトの気持ちが非常に大きくなりました。
当たり前のように使ってきたものがどれだけ有難いものなのかを実感した旅でした。
もっともっと自然とそこから生まれる材料やそれをつくる人々へ思いを馳せて家づくりをしていこうと思いました。
北海道旅、最高でした!
【その他の関連記事】
無垢フローリングのルーツを辿り北海道へ。研修レポート前編~植林体験~
「無垢材」を使ったリフォーム・リノベーション施工事例一覧